
Les gueuses à la sortie de la fonderie
(Image Mécilor)
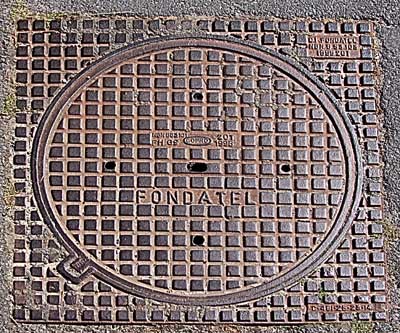
La fonte est utilisée pour le mobilier urbain comme des bouches d'égout
|
---|
La fonte est produite dans un haut fourneau. La fonte de première fusion est appellée "pig iron" (fer de cochon) dans les pays anglo-saxons. Historiquement, la coulée se faisait au pied du haut fourneau dans un moule de forme ramifiée: vu d'en haut, on dirait une truie qui allaite ses jeunes, de là le nom. Plus tard, la fonte a été coulé dans des moules dans un batiment séparé. On produit des "gueuses" (de l'allemand 'Gies', le résultat de la coulée) ayant la forme d'un lingot irrégulier. Actuellement, la fonte est transportée sous forme liquide dans des torpilles vers l'aciérie (pour la transformer en acier) ou vers une fonderie (pour en faire des pièces moulées).
La fonte la plus courante est la fonte phosphoreuse produite à partir de minérai qui contient du phosphore (comme la minette lorraine). Cette fonte est de moindre valeur en aciérie, car elle nécessite un traitement plus poussé. La fonte hématite est produite avec du minérai de meilleure qualité (de l'oxyde de fer pratiquement pur).
La fonte en fusion contient du carbone en solution, qui va se séparer et former des cristaux microscopiques quand la fonte se solidifie. C'est la quantité et le type de ces cristaux qui déterminent les caractéristiques de la fonte.
La plus grande partie de la production de fonte est transformée en acier.
Seconde fusion dans le cubilot
Les gueuses sont transportées vers la fonderie où elles seront refondues dans un cubilot (haut fourneau miniature) pour la fabrication de pièces moulées: bouches d'égout et autre mobilier urbain, carter de moteur automobile, bâti de machines, installations de chauffage (de la chaudière aux radiateurs en passant par les poêles à charbon). Les installations de chauffage en fonte (poëles et radiateurs) accumulent la chaleur. Il y a 100 ans, une grande partie de la production d'un haut fourneau était utilisé sous forme de fonte.
Alors qu'au début de l'ère industrielle, la fonte était utilisée telle quelle, maintenant on fait subir une seconde fusion qui servira également à la purifier. On ajoute certains fondants dans le cubilot pour obtenir exactement la fonte voulue. Il s'agit souvent de la castine (du flamand 'kalksteen', pierre d'argile). L'argile va absorber les impuretés et flotter à la surface de la fonte en fusion.
On y ajoute des éléments qui donneront des particularités spéciales à la fonte: il est ainsi possible de faire des villebrequins en fonte spéciale. Ces fontes n'ont plus les inconvénients de la fonte classique et il est même possible de la travailler pour lui donner une forme complèxe.
Caractéristiques de la fonte
Contrairement à l'acier qui devient ductile à chaud et peut être travaillé, la fonte passe de l'état solide à l'état liquide un peu comme un glaçon qui fond. La fontes est extrèmement dure, mais cassante: il n'est donc pas possible de laminer ni d'usiner la fonte (sauf certaines fontes spéciales comme la fonte ductile).
La fonte est très solide, absorbe bien les chocs, ne rouille pas. Le moulage de pièces de métal est plus rapide que les autres formes d'usinage. Malheureusement, la fonte est cassante, ne peut pas se travailler ni se souder. Les pièces moulées sont relativement grossières. On remplace la fonte de plus en plus souvent par des tôles d'acier (plus fines, et donc meilleur marché).
La fonte est toujours utilisée pour certaines pièces de matériel urbain (plaques et grilles d'égout,...) car elle ne s'use pratiquement pas. Il s'agit ici de fonte GS (graphite sphéroïdal) qui combine les avantages de la fonte et de l'acier.
Un font en fonte d'une longueur de 35m, fabriqué en 1791. A cette époque, l'acier était très rare (on ne trouvait que du fer forgé) car il n'existait pas de procédés industriels valables pour transformer la fonte en acier.
La fonte résiste très bien à la compression, tout comme la pierre (remarquez la forme caractéristique du pont). Mais la fonte n'est pas élastique et de nombreux ponts mal étudiés se sont effondrés.
|