Avant de nous pencher sur l'avenir des hauts fourneaux, un petit rappel du fonctionnement d'un haut fourneau s'impose.
Le minerai de fer (chimiquement de l'oxyde de fer) est introduit en haut du fourneau. Il se réchauffe au contact des gaz brulants ascendants.
- A 400° il a perdu toute son humidité (dessication)
- A 800° il est réduit en fer pulvérulent (réduction)
- A 1200° il est transformé en fonte (carburation)
- A 1600° il se liquéfie et est récolté au creuset (fusion)
Comme gaz réducteur, on utilise principalement du monoxyde de carbone, produit par la combution incomplète du coke. La combustion du coke produit également la chaleur nécessaire.
La Belgique était un des plus grand fabricants d'acier en 1970 (9me producteur mondial). Une production importante est possible avec un nombre restreint de haut fourneaux qui donnent aussi de l'emploi à différents secteurs en amont (préparation du minerai, du cokes et des fondants) en en aval (transformation de la fonte en différentes sortes d'aciers).
Le haut-fourneau a quelques inconvénients majeurs:
- Il utilise du coke, un produit de base dont le prix de fait qu'augmenter avec la réduction de la quantité de houille cokéïfiable.
- Le régime de fonctionnement est fixe: le four produit 10.000 tonnes par jour. Pour des raisons d'économie d'échelle, pas possible de construire des "petits fours".
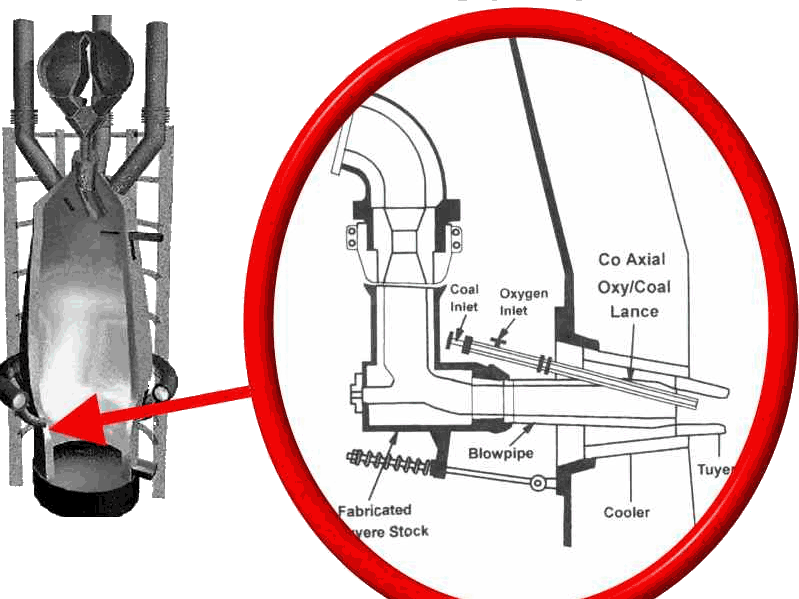
Injecteur d'oxygène et de poudre de charbon
|
---|
La sidérurgie a commencé avec le procédé de réduction directe!
En effet, le fer ne devient jamais liquide dans un bas fourneau. Comme quoi, la vie est un éternel recommencement...
|
|
---|
Pour réduire la consommation en coke on a équipé les fourneaux d'injecteurs de carburant (d'abord du fuel lourd (bunker oil), puis de la poussière de charbon). Le charbon coûte moins cher que le coke et est injecté aux tuyères, là où la température doit être la plus élevée. Le charbon est injecté simultanément avec de l'air fortement enrichi en oxygène (pour éviter que l'azote de l'air qui n'a aucune fonction ici ne refroidisse le four).
On peut également augmenter légèrement le rendement en injectant non plus de l'air surchauffé, mais de l'oxygène plus ou moins pur. On se limite a un taux d'enrichissement de 5%, car l'azote sert à transporter l'énergie calorifique dans les étalages et à maintenir la charge suffisamment aérée. Une charge trop tassée par manque de circulation d'air peut former une voûte et se bloquer. La “chute en marche” provoque généralement une explosion dans le four avec fonctionnement du clapet de sécurité et refoulement des matières du creuset (fonte et laitier) vers les tuyères.
Et puis on c'est dit... Ce qu'on recherche, c'est de l'acier, pas de la fonte (dans l'aciérie, la fonte est transformée en acier par brassage avec une lance à oxygène). Et le fer, ... il n'a pas vraiment besoin d'être liquide.
Et c'est ainsi qu'on a effectué des recherches dans la réduction directe. Les nouveaux fours n'ont que la phase 1 et 2. Passé la phase 2, le minerai est simplement refroidi par un courant d'air et est récolté en bas du four sous la même forme qu'à l'entrée. Souvent on en profite pour comprimer le fer encore chaud sous forme de boulettes (voir dernière photo)
L'énergie provient généralement du gaz naturel. Le gaz est brulé avec un manque d'oxygène dans un échangeur de chaleur séparé. Les gaz chauds qui contiennent principalement du monoxyde de carbone et de l'hydrogène sont fortements réducteurs et sont envoyés à mi-hauteur dans le fourneau.
Les gaz issus du fourneau sont recyclés et menés dans des catalyseurs où la vapeur d'eau (provenant de la calcination du minerai de fer) est transformée en hydrogène. Cet hydrogène est de nouveau utilisé dans le four.
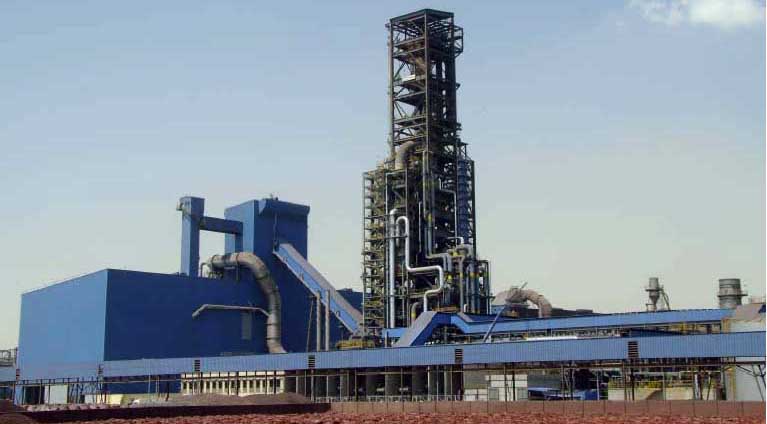
Four de type Midrex
Le four peut être plus petit (un débit minimal n'est pas nécessaire pour garantir un fonctionnement économique), n'a pas les conduits typiques de récupération des gaz brulés et le fer est récolté sous forme pulvérulente à la base du four. Le four travaille à une température plus basse et les réactions chimiques sont donc moins violentes (c'est parfait pour le revètement du four). La capacité de production est moindre en comparaison d'un haut-fourneau classique et on a remplacé le coke par du gaz naturel. Tout autre carburant à base d'hydrocarbures fait l'affaire car le réacteur (où se produit la réduction du minérai) est séparé du foyer.
Un fourneau de type Midrex est plus souple qu'un haut fourneau classique, non seulement par le choix du carburant (qui produit le gaz réducteur), mais la production journalière peut être adaptée à la demande. Le taux de carbone dans le fer récolté dépend du rapport monoxyde de carbone/hydrogène du gaz réducteur injecté dans le réacteur.
Le fourneau Midrex n'a pas que des avantages: comme le fer ne passe jamais en fusion, il ne peut se séparer de la gangue. Seul les minerais les plus purs (hématite) peuvent servir dans ce type de four.
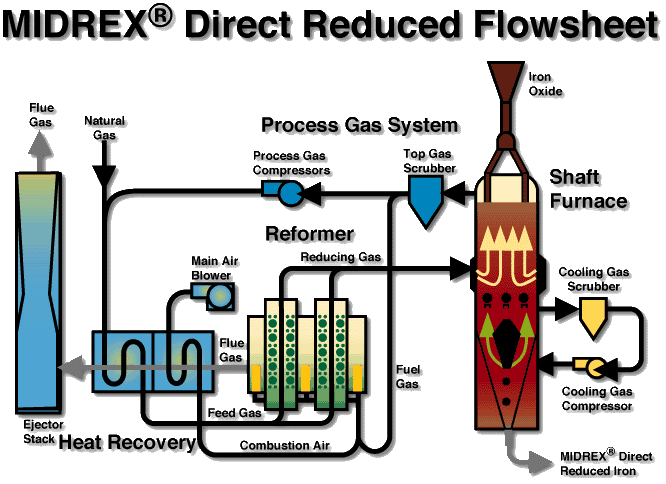
Procédé Midrex
La forme du four n'est pas limitée à un haut fourneau, et différents systèmes sont à l'étude: lit fluidifié, anneau circulaire, four horizontal rotatif, etc. Il ne s'agit maintenant plus d'un fourneau classique mais d'un réacteur chimique.
Le fer issu d'un fourneau à réduction directe doit être traité rapidement car sa forme pulvérulente le rend très réactif (dans certaines circonstances, il peut même s'enflammer spontanément). Expoé à l'air humide, il se transforme rapidement en rouille et le cycle est à recommencer. Le fer est laminé et utilisé tel quel ou sert de materiau de base dans la métallurgie en poches.
|