L'usine sidérurgique d'Athus est décrite plus en détail ici. Il ne reste plus rien de l'usine: sauf un petit monument où se trouvait l'entrée de l'usine. Il ne reste plus que le musée Athus-Acier.
3 Le musée "Athus et l'Acier"
Ce sont des bénévoles qui tiennent le musée. Il y a différentes salles montrant le fonctionnement de l'usine. Il y avait dans l'usine tout ce qu'il y a dans une usine dix fois plus grande: la procédure générale d'affinage de l'acier est restée la même, sauf que les procédés sont devenus plus efficaces par économie d'échelle.
Le petit film qui est montré est assez unique: il montre la production d'acier dans les années 1950.
1 2 3 4
Au musée:
Petite démonstration mécanique de la fabrication de l'acier:
- Le versement de la fonte en fusion dans le mélangeur et à coté le versement de la fonte de la poche dans le convertisseur Thomas
- Déversement d'une partie de la fonte du mélangeur dans une poche et soufflage du convertisseur: on en est à la fin de l'opération de soufflage avec apparition de grosses volutes rousses (oxyde de fer)
- Déversement de l'acier: on verse d'abord les scories qui flottent à la surface de l'acier (elles seront utilisées comme engrais) et puis on verse l'acier dans une lingotière. Un lingot est envoyé au laminage
- Opération de laminage. Au bas de l'image on voit un dex gros rouleaux qui servent à étirer le fil pour faire des ronds à béton. Les ronds à béton ne sont pas lisses mais striés: les stries permettent une meilleure adhérence du béton.
5 6 7
Vues du musée:
Chaque salle reprend une partie de l'activité de l'usine: l'infirmerie, le bureau du directeur et une des grandes salles où on voit les matières premières et les produits finis, mais également les appareils utilisés.
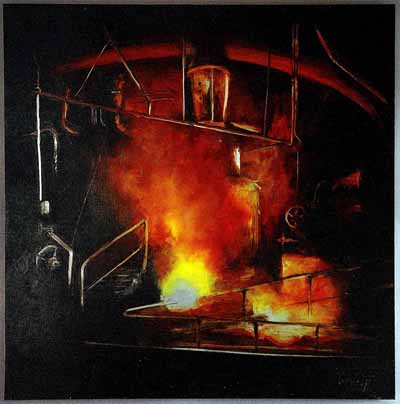
Il y a évidemment plusieurs peintures dans le musée. Elles reprennent des vues de l'aciérie d'Athus, mais également de Rodange.
Les documents à droite sont extraits de la documentation présente au musée.
8 9
Haut fourneau:
Coupe d'un haut fourneau montrant ses parties caractéristiques:
- le gueulard où sont introduites les matières premières. Les premiers hauts-fourneaux n'étaient pas fermés, les fourneaux plus récents (à partir de la seconde guerre mondiale) étaient fermés par le dessus. On pouvait ainsi récolter le gaz de haut fourneau qui était combustible. Ce n'est pas un combustible très efficace, mais un four en produit de très grandes quantités. Pour obtenir une température de flamme supérieure à 1000° il fallait y ajouter du gaz naturel.
- C'est dans la cuve que s'entassent les matières premières (alternativement une couche de cokes et de minérai prétraité). La température monte au fur et à mesure que la charge descend. La cuve s'élargit pour permettre une descente de la charge sans à-coups. Le coke qui brule extrait l'oxygène du minérai qui se transforme en fer.
- Au ventre, la température devient si élevée que le fer devient pateux et puis liquide. Il se sépare de la gangue qui forme le laitier.
- Dans les étalages il y a une réduction du volume, c'est pour cela que le four rétrécit. Le four plus étroit à cet endroit permet de mieux concentrer les réactions chimiques. Il faut ici que la température soit la plus élevée. Le fer pateux absorbe du carbone et devient de la fonte qui est plus liquide.
- La fonte s'accumule dans le creuset et le laitier surnage. Un trou de coulée permet de faire sortie la fonte en fusion. Certains fours utilisent un seul trou de coulée (c'est d'abord la fonte qui s'écoule et puis le laitier), d'autres fours utilisent deux trous à des hauteurs différentes. Une fois la coulée terminée, le trou est bouché jusqu'à la coulée suivante.
- L'air surchauffé est injecté sous forte pression au dessus du creuset par des tyuyères.
Le plan suivant montre les dimensions du four. La hauteur totale est de 30m. Les fours sont donc relativements petits. Comme la surface est importante par rapport au volume, ils ont un rendement moindre (plus de pertes de chaleur) et nécessitent donc plus de cokes qu'un four plus grand.
10
Cowper:
Un haut fourneau a deux ou trois cowpers. Ils sont décrits plus en détail sur cette page. Ce sont de grands accumulateurs de chaleur.
Un cowper est en phase vents: l'air froid est insufflé dans le cowper (flèche bleue), l'air s'échauffe en montant dans le ruchage. L'air chaud (flèche rouge) va alimenter le haut fourneau. Dans un haut fourneau moderne, la température de l'air peut atteindre 1200°: le rendement du four est donc très bon car il ne nécessite que peu de cokes comme carburant.
Ici, la température de l'air chaud n'atteignait qu'environ 1000°. La raison est qu'il n'y avait que deux cowpers par four, le cowper en phase gaz n'a pas le temps de chauffer assez fort (dans un four plus récent, il y a deux cowpers en phase gaz).
Il y a un bruleur qui brule le gaz de haut fourneau additionné de gaz naturel. Le gaz monte et puis passe par les ruchages et perd sa chaleur (flèches violettes).
11
Convertisseur Thomas:
Le convertisseur Thomas convertit la fonte en acier et élimine également certaines impuretées qui s'échappent soit sous la forme de gaz, soit se retrouvent dans le laitier.
Le convertisseur a un fond percé par où est injecté l'oxygène pour la conversion. Pour limiter la température, on injecte également du gaz naturel qui par craquage va absorber une partie de la chaleur exédentaire. Les grands convertisseurs injectent l'oxygène par le haut et les tuyères ne servent que pour l'injection de gaz argon, qui produit un mélange de la fonte dans le convertisseur.
D'abord le convertisseur est rempli avec une petite quantité d'acier de récupération (chutes qui qui proviennent du laminage). L'acier en fondant va absorber la chaleur exédentaire. Il est donc important de controler exactement la quantité d'acier qu'on ajoute.
On ajoute ensuite la fonte, on redresse le convertisseur et on commence le soufflage. Les composants indésirables de la fonte sont pxydés. En dernier lieu on a l'oxydation du phosphore. Quand le phosphore est oxydé, c'est le fer qui commence à être oxydé (fumées rousses) et il faut stopper le soufflage.
Le convertisseur bascule à nouveau et on récolte le laitier qui sera utilisé comme engrais (il contient beaucoup de phosphore). On récolte ensuite le fer pratiquement pur dans une poche. C'est du fer doux qui n'est pas utiliser tel quel. Le fer ne contient plus de carbone et il faut en ajouter via de l'anthracite pour faire de l'acier. On ajoute également des métaux d'alliage qui vont donner les caractéristiques voulues à l'acier: c'est la métallurgie en poche.
Si les musées de l'industrie vous interessent, consultez également la page consacrée aux musées de l'industrie.
|